The effectiveness and longevity of hydraulic systems heavily rely on the condition and performance of their components, with seals playing a pivotal role. The process of hydraulic motor seal replacement is a task that requires meticulous attention to detail, combining the understanding of mechanical systems with the expertise to execute precise interventions. This critical guide explores the nuances of this procedure, offering professional insights to ensure optimal performance and reliability.
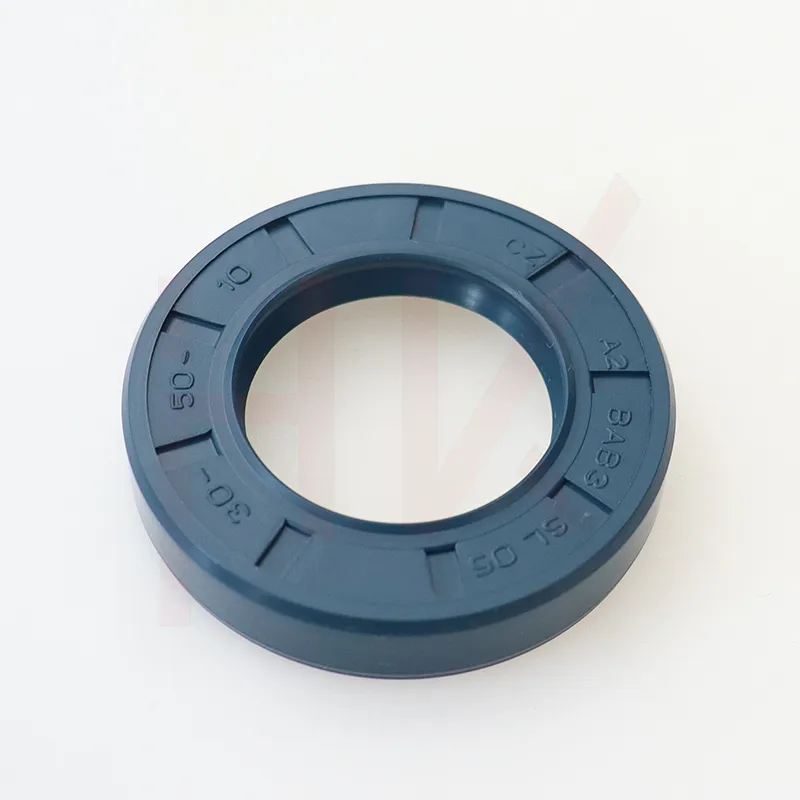
Hydraulic motors are essential for converting hydraulic energy into mechanical power, driving countless industrial and mobile machinery applications. Central to their operation are seals, which maintain pressure, prevent fluid leaks, and protect internal components from contamination. Over time, these seals can wear out, harden, or even break, leading to inefficiencies and potential system failures. Recognizing the signs of faulty seals early on, such as diminished performance, unusual noises, or visible fluid leaks, is crucial for preventing significant downtime or damage.
The initial step in replacing a hydraulic motor seal involves a thorough system diagnosis. By using pressure gauges, fluid analysis, and visual inspections, one can confirm that the seal is indeed the source of the issue. Attempting a replacement without proper diagnostics can lead to oversight of other potential problems. It's also essential to understand the type of seal used — whether it’s an O-ring, lip seal, or T-seal, as each has distinct handling and installation requirements.

Once identified, preparing the workspace and gathering necessary tools is imperative. The environment should be clean and well-organized to prevent any contaminants from entering the system during the replacement process. Necessary tools typically include seal picks, screwdrivers, and protective covers, along with the new seals. Having the manufacturer’s manual on hand is beneficial, providing specific instructions and safety guidelines tailored to the particular motor model.
Dismantling the hydraulic motor requires meticulous technique to avoid damage to delicate components. Safely relieving the system of pressure before disassembly is non-negotiable to ensure safety. References to the motor’s manual aid in following the correct sequence of disassembly, preventing unnecessary stress on parts. Careful labeling or photographing components during this stage can alleviate the reassembly process, confirming proper placement of each element.
hydraulic motor seal replacement
Removing the old seals demands both patience and precision. Utilizing appropriate tools, such as seal picks, facilitates the removal without causing abrasion to the seating surface. If the old seal proves stubborn, applying a gentle heat source can sometimes soften the material for easier extraction. Cleaning the seal groove is vital once the old seal is removed, ensuring no debris contaminates the new seal's installation area.
Selecting the correct seal replacement is a decision best informed by thorough knowledge. Factors like material compatibility and seal design are crucial; seals may be made from nitrile, fluorocarbon, or other specialized materials based on use conditions. Cross-referencing with manufacturer specifications guarantees matching the parameters for pressure, temperature, and medium compatibility, thereby ensuring reliable performance post-installation.
With the new seal ready, proper lubrication is critical. Lightly lubricating the seal with a compatible hydraulic fluid helps in easy insertion and minimizes installation damage. While the temptation might be to stretch the seal over components, careful seating without excessive force ensures longevity and function. Special attention is required to align seals evenly to prevent malfunctions once the system is operational.
Finally, assemble the motor in reverse order of disassembly, keeping in mind precision in alignment to avoid misfires. This step should be executed with as much care as the dismantlement, ensuring no parts are left loose or incorrectly placed. Performing a pressure test upon reassembly ensures that seals are seated correctly, confirming leak-free operation and establishing full system efficiency.
Hydraulic motor seal replacement is a task that demands both technical knowledge and hands-on expertise. Proper execution not only restores motor efficiency but also extends component lifespan, reducing maintenance costs and preventing unscheduled downtime. By approaching this task with attention to detail and adherence to best practices, you set the foundation for hydraulic system durability and operational success.