Hydraulic gear pump seals play a pivotal role in the efficiency and longevity of hydraulic systems, especially in the industrial and machinery sectors. These components are crucial in ensuring that your hydraulic gear pumps maintain optimal performance and avoid unexpected breakdowns that can lead to costly downtime.
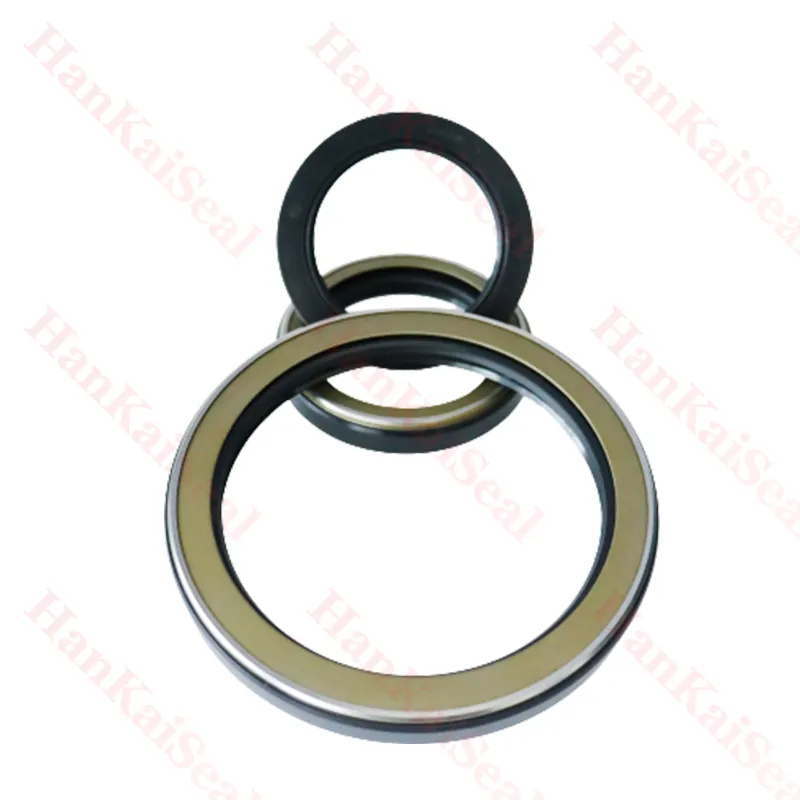
The vital function of hydraulic gear pump seals is to ensure that hydraulic fluids remain contained within the pump housing. This containment is essential to maintain appropriate pressure levels and prevent the ingress of contaminants that can compromise the fluid’s integrity. An effective seal helps eliminate leaks, which can not only cause performance issues but also pose environmental and safety hazards.
One of the primary considerations when selecting hydraulic gear pump seals is material compatibility. Seals are often subjected to rigorous conditions, including extreme temperatures, pressures, and exposure to various hydraulic fluids. As such, choosing a seal made from a material that can withstand these conditions is critical. Common materials include nitrile rubber (NBR), fluoroelastomers (FKM), and polyurethane. Each has its strengths NBR offers good abrasion resistance, FKM is excellent for high temperature and chemical stability, and polyurethane provides exceptional resistance to wear and tear.
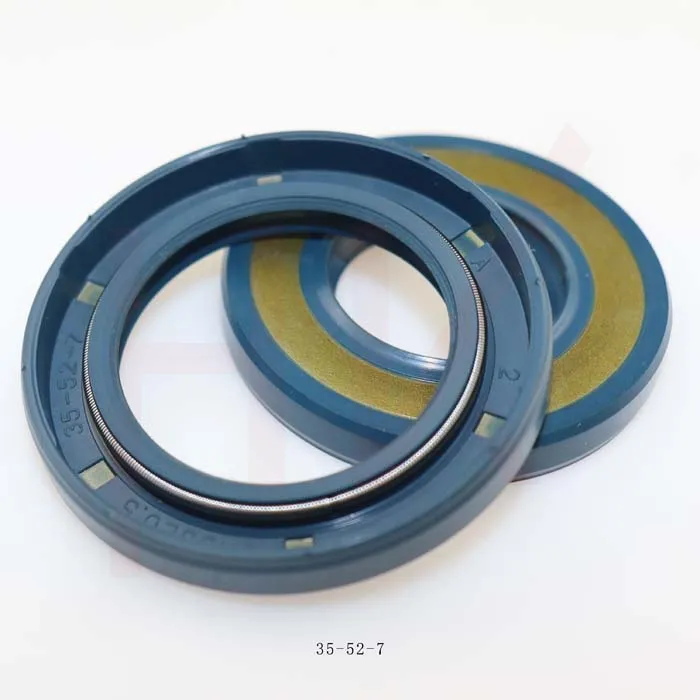
When installing hydraulic gear pump seals, precision is important. An improperly fitted seal can lead to leaks and pump inefficiency. Therefore, ensuring that seals are correctly installed following the manufacturer's guidelines is crucial. This not only improves the lifespan of the seal but also enhances the overall reliability of the hydraulic system.
It is also important to recognize the early signs of seal failure.
Common indicators include hydraulic fluid leaks, abnormal noise from the pump, and decreased system performance. Promptly addressing these issues by inspecting and replacing seals can save significant repair costs and prevent further damage to the pump.
hydraulic gear pump seals
One of the advancements in hydraulic gear pump seals technology is the development of seals with enhanced wear resistance and durability. Innovative designs and materials now offer seals that can withstand higher pressures and temperatures. This progress in seal technology facilitates longer intervals between maintenance cycles, thereby reducing operational costs and improving efficiency.
From an expert's perspective, regular maintenance and inspection routines should integrate checks for seal integrity. Industry professionals often recommend establishing a routine seal replacement schedule based on the specific operating conditions of the pump and the material properties of the seal. These practices not only help in maintaining the optimal function of the hydraulic system but also in extending the lifespan of its components.
Building trust and reliability in hydraulic gear pump operations is contingent upon consistent performance, which is directly influenced by seal quality. Investing in high-quality seals may have a higher initial cost, but the long-term benefits in terms of efficiency, reliability, and reduced downtime make it a wise investment.
Leveraging the latest advancements in seal technology and adhering to regular maintenance schedules can significantly enhance the performance and reliability of hydraulic gear pumps. For businesses operating in sectors that rely heavily on hydraulic systems, such as construction, manufacturing, and agriculture, the dependable operation of these systems is non-negotiable.
In conclusion, understanding the critical role of hydraulic gear pump seals and taking a proactive approach in their selection, installation, and maintenance can result in substantial improvements in system efficiency and cost savings. Through the expertise and insights offered by professionals in the field, businesses can ensure their hydraulic systems operate smoothly, maintaining the balance between performance and sustainability.