In the intricate world of machinery and automotive functionality, the seemingly inconspicuous oil seal plays a pivotal role. As industry professionals and enthusiasts often underline, an oil seal's primary function is safeguarding against the ingress of dirt and the escape of lubricants. Let’s navigate the crucial aspects of the size designation 14 22 5 oil seal, a critical component for diverse equipment and machines, focusing on its functionality, selection criteria, and practical applications.
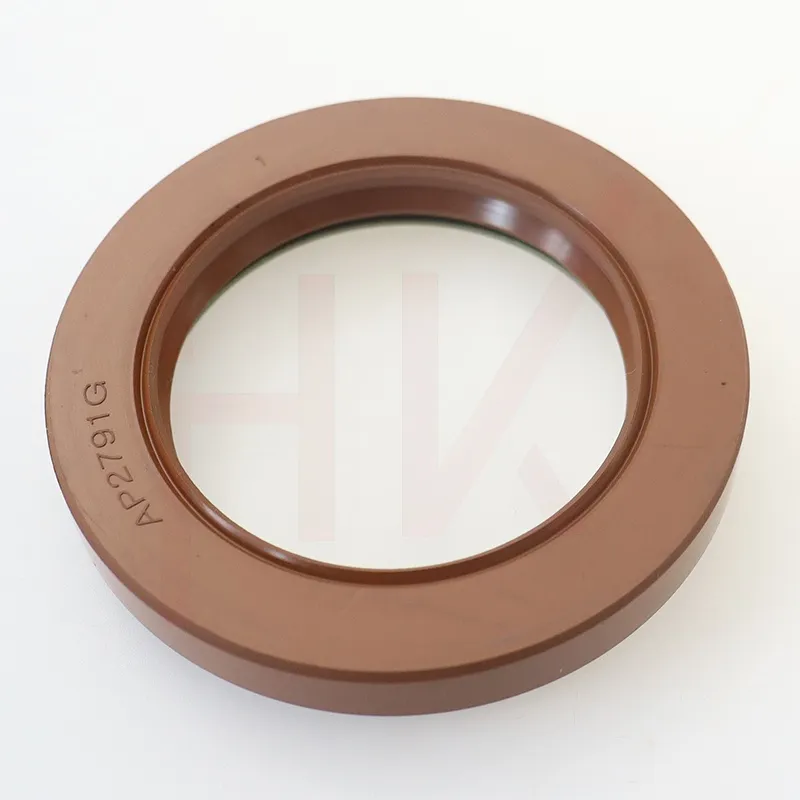
Oil seals, at their core, contribute to the seamless operation of rotating, reciprocating, and oscillating shafts. The 14 22 5 in an oil seal specification represents the critical dimensions 14mm inner diameter, 22mm outer diameter, and 5mm width. These sizes must align precisely with the application requirements to ensure optimal performance. Mismatched dimensions could lead to leaks or seal failure, both of which can cause premature wear or damage to machinery components.
Durability and performance are paramount in evaluating an oil seal's expertise. Material selection, an often-overlooked factor, ties directly into performance. Materials like nitrile rubber (NBR) are favored for general purposes due to their balanced resilience and affordability. For applications demanding high thermal resistance, such as automotive engines, silicone or fluorocarbon seals provide superior performance. Selecting the correct material that withstands specific operational temperatures and chemical exposure is essential for long-term reliability.
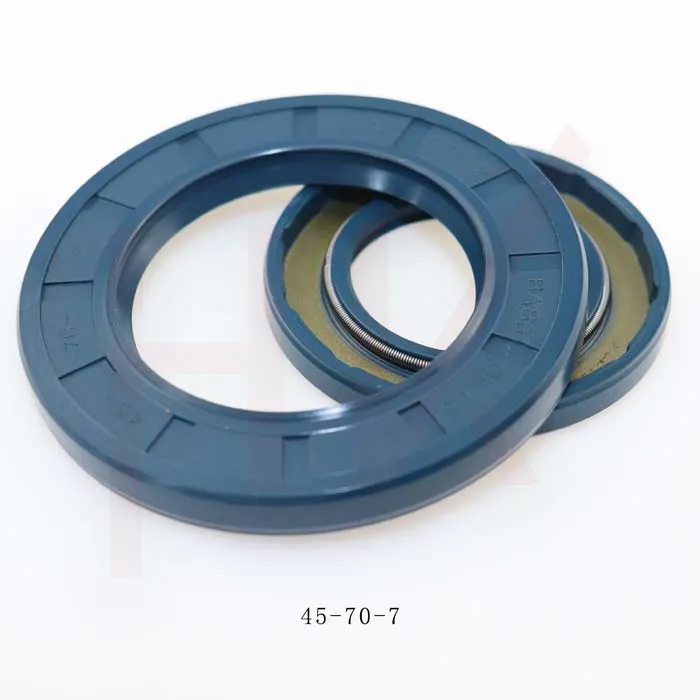
In deploying 14 22 5 oil seals, the implementation technique warrants attention. Experts assert that proper installation involves clean, undamaged surfaces and the use of appropriate tools to prevent distortion or wear during fitting. Misalignment or physical damage during installation often leads to compromised seal integrity.
Frequently, the operational environment dictates unique demands on these seals. In dusty or dirty surroundings, enhanced seal design with auxiliary dust lips can offer additional protection, extending the service life. The right design mitigates external contamination, a critical factor affecting productivity and maintenance cycles.
14 22 5 oil seal
The authoritative knowledge around 14 22 5 oil seals also encompasses regular maintenance protocols. Inspections for signs of wear, such as hardening, cracking, or discoloration, are necessary to avert unexpected equipment failures. Consistent monitoring aids in deciding precise replacement intervals, directly impacting the machine's reliability and efficiency.
Trustworthiness in the use of oil seals is established through adherence to manufacturer guidelines and industry standards. Reputable manufacturers often provide specifications and guidance, fostering confidence and ensuring that every piece of the machinery functions cohesively. Leveraging this foundational knowledge affords users the ability to diagnose issues preemptively and effectively, a testament to both foresight and practiced technical acumen.
Furthermore, real-world experience underlines the practical application of oil seals in diverse industries, from automotive to manufacturing to aerospace.
The adaptability of the 14 22 5 size oil seal renders it invaluable across these sectors. In racing engines, for example, the seal’s role is amplified due to high temperatures and vigorous conditions, underscoring the need for precision and quality materials.
To encapsulate, selecting the appropriate 14 22 5 oil seal significantly impacts machinery’s longevity and efficiency. Understanding the interplay between material selection, environment, and maintenance empowers users to make informed decisions, ensuring seamless operation and minimizing downtime. As the market demands evolve, the insight provided by industry experts and new technological advancements continuously redefine the limits of seal applications, maintaining these components as the unsung heroes of intricate mechanical systems.