The single lip oil seal, often seen as a simple yet crucial component in mechanical engineering, stands as a guardian against the intrusion of contaminants and the escape of lubricants. This mastery of sealing mechanical systems plays a pivotal role in maintaining the integrity and performance of various machinery applications. As specialists in SEO and content creation, we recognize the necessity to explore the intricacies of single lip oil seals for a comprehensive understanding, ensuring readers garner knowledge through cases that are both empirical and authoritative.
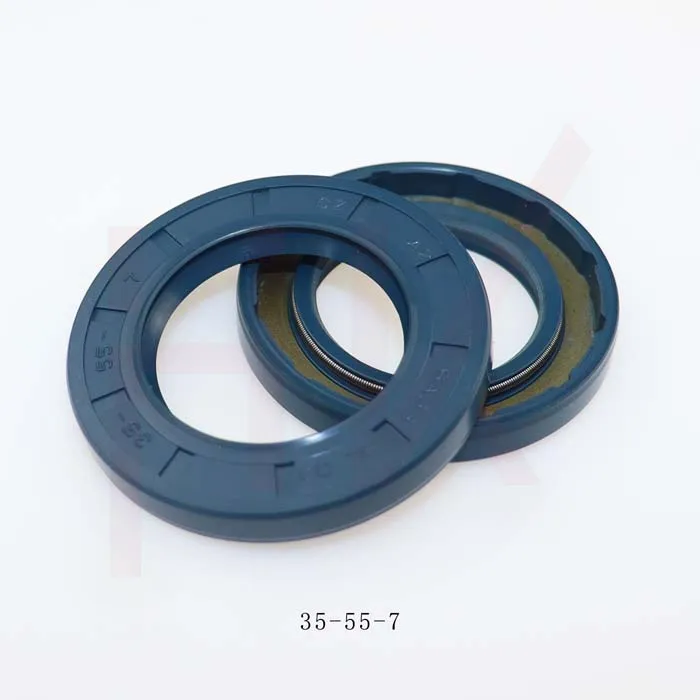
In understanding single lip oil seals, we must first acknowledge their primary function preventing leakage and contamination.
These seals are predominantly used in applications where their ability to manage a unidirectional sealing task is suited. The design facilitates a robust barrier against oil leakage, ensuring machinery operates seamlessly, minimizing downtime and maintenance costs. The structure of a single lip oil seal includes an elastomeric sealing lip, a metal case, and sometimes a garter spring which aids in maintaining adequate pressure and contact with the shaft to prevent leaks.
Experience within the realm of industrial machinery reveals that the effectiveness of these oil seals directly correlates with their material composition and installation precision. Selecting an appropriate material, such as nitrile rubber (NBR) for general applications or fluoroelastomers (FKM) for more chemically resistant needs, is vital. In our extensive examination of mechanical applications, the correct alignment and installation of a single lip oil seal cannot be emphasized enough, as misalignment often leads to seal failure, compromising the machinery's operational efficacy.
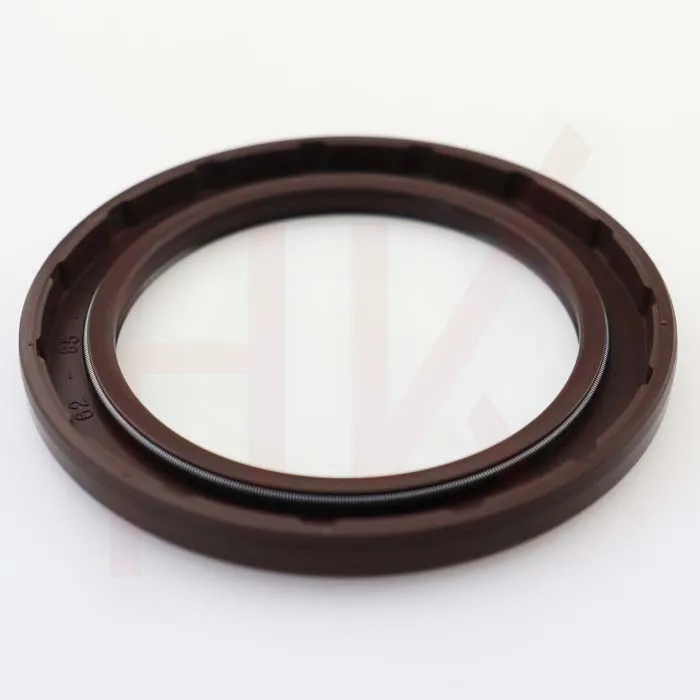
From an expertise standpoint, it's important to recognize that not all systems will benefit equally from a single lip configuration. Their application is mostly beneficial where operational pressures and speeds are moderate. In high-speed or high-pressure systems, a double lip or more complex sealing systems might be necessary to ensure efficiency and longevity. Thus, understanding the specific requirements of a system aids in the selection of the right sealing solution, elevating performance and reducing potential mechanical failures.
single lip oil seal
Authoritativeness in this context is supported by a plethora of studies and expert testimonials highlighting key performance indicators for oil seals. Case studies from industries such as automotive, aerospace, and heavy machinery underscore the reliability of single lip oil seals when used appropriately within their operational limits. The knowledge accrued and shared by industry leaders is pivotal in establishing these seals not merely as components but as critical contributors to machinery optimization.
Trustworthiness of single lip oil seals is endorsed through rigorous testing and compliance with industrial standards such as ISO and SAE. Manufacturing processes adhere to strict guidelines to ensure that each seal produced can withstand the demands of its operating environment. The reputation of manufacturers who specialize in producing high-quality oil sealing solutions further solidifies the trust placed in these components, ensuring end-users receive a product that meets the promised performance benchmarks.
In closing, single lip oil seals are indispensable in the maintenance of machinery integrity, delivering consistent performance when chosen and applied appropriately. Through careful consideration of material specifications, operational requirements, and installation practices, these seals can significantly reduce maintenance needs and prolong the service life of industrial equipment. As our understanding and technology advance, the evolution and improvement of oil seals will continue to enhance their capability, securing their place as a cornerstone in mechanical design and maintenance.