Hydraulic cylinders are integral components in various industrial machinery, contributing to processes requiring precise linear motion and force. However, maintaining their optimal function necessitates regular upkeep, including replacing the wiper seal. This seemingly minor component plays a crucial role in protecting the internal mechanisms from contaminants while ensuring the smooth operation of the cylinder.
Here’s an expert guide on replacing the wiper seal, drawing from years of specialized experience and industry best practices.
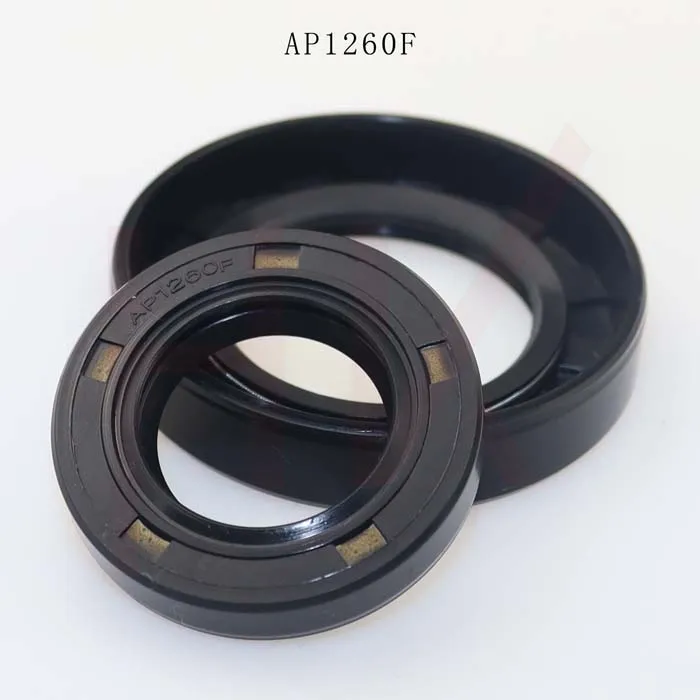
Understanding Wiper Seal Functionality
A wiper seal's primary function is to prevent dust, dirt, and debris from entering the hydraulic system. It sits at the cylinder’s outer end, helping to safeguard the internal components against contamination that could lead to wear and reduced efficiency. Regular inspection and timely replacement of the wiper seal are critical in extending the lifespan of the whole hydraulic system.
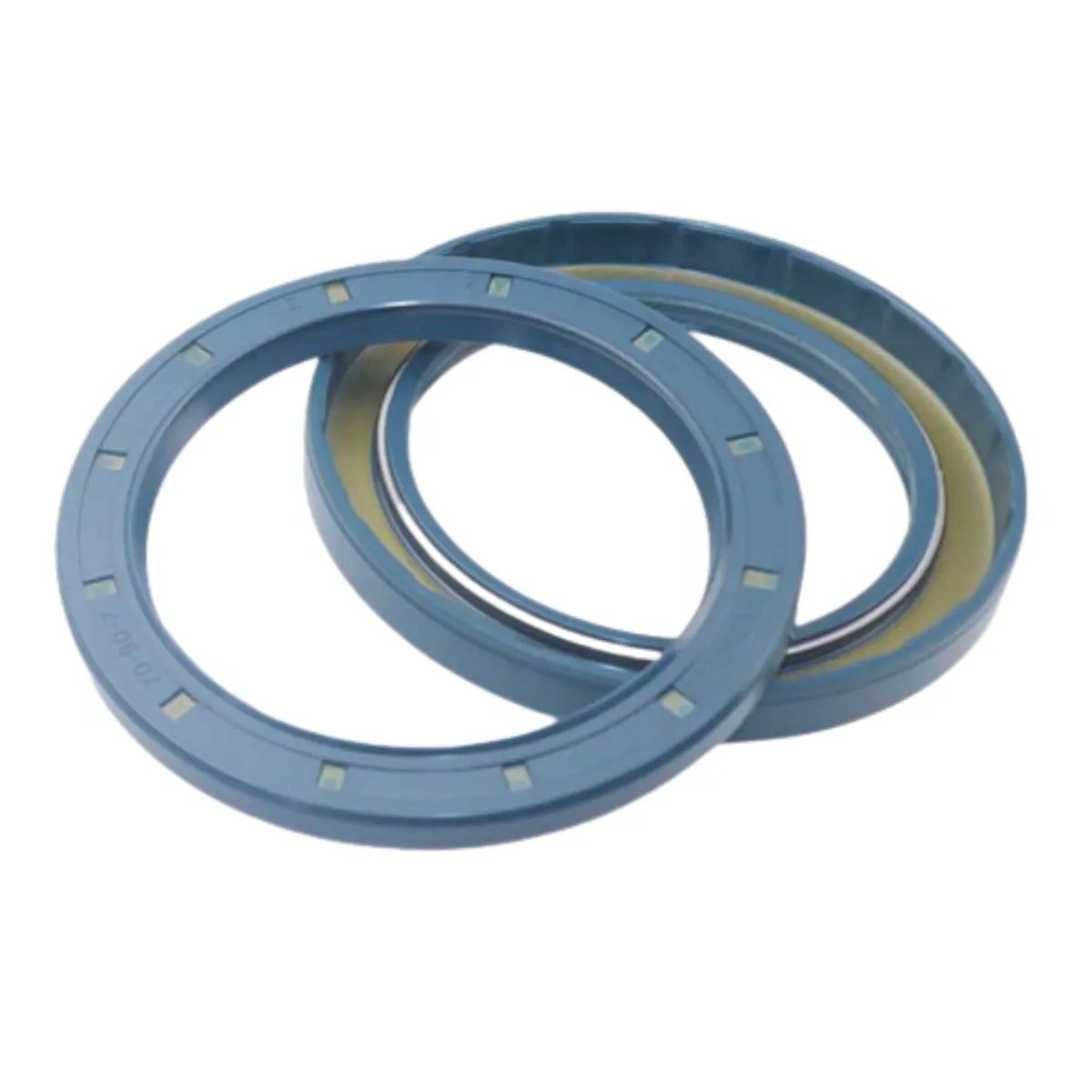
Identifying the Need for Replacement
Indicators for wiper seal replacement include visible wear, such as cracks or deformities, and signs of contamination within the hydraulic fluid. Additionally, leakage or unusual noises during operation may signify a compromised seal. Conduct thorough inspections during routine maintenance checks to catch these symptoms early.
Pre-Replacement Preparations
Before beginning the wiper seal replacement process, ensure you have all necessary tools and parts ready. This includes a replacement seal compatible with your hydraulic system, wrenches, screwdrivers, lubricant, and a cleaning cloth. It is essential always to consult the hydraulic cylinder’s manual for specifications to avoid using inappropriate parts or procedures that could harm the system.
Step-by-Step Replacement Process
1. Safety First Ensure the machinery is entirely shut down and depressurized. Lock out and tag out all energy sources to prevent accidental startup during maintenance.
replacing wiper seal on hydraulic cylinder
2. Access the Wiper Seal This usually involves removing protective covers and disconnecting any adjacent components obstructing access to the seal. Keep all removed parts in sequence for easier reassembly.
3. Seal Removal Carefully extract the worn seal using the appropriate tools to avoid damaging the surrounding area. Some seals require specific extraction tools provided by the manufacturer.
4. Inspection and Cleaning Inspect the seal groove and adjacent parts for damage or excessive wear. Clean the area with a lint-free cloth and appropriate cleaning solution to remove any residual contaminants.
5. Install the New Seal Lubricate the new seal lightly to facilitate insertion. Follow the manufacturer’s instructions to position the seal correctly, ensuring it sits snugly within the groove.
6. Reassemble the Components Carefully reattach all previously removed parts, ensuring each is secured and aligned properly to prevent operational issues.
7. Testing Gradually re-pressurize the system and perform initial operations to ensure the new wiper seal is functioning correctly without leaks or unusual noises.
Trust and Reliability
Performing regular maintenance such as wiper seal replacement not only ensures the reliability of hydraulic machinery but also builds trust in operational consistency. As professionals in the field, acknowledging the nuances of this process showcases expertise and reinforces authority on best maintenance practices. Users can rely on well-maintained equipment to deliver predictable performance, thereby reducing downtime and associated costs.
For organizations and technicians, investing in the right tools, following precision guidelines, and using quality replacement components are crucial for maximizing machinery lifespan and efficiency. These deliberate efforts reflect a commitment to excellence and reliability in an ever-demanding industrial landscape.