Hydraulic oil seals play a vital role in ensuring the seamless operation of hydraulic systems across various industries. While often overlooked, their influence on machinery's efficiency, lifespan, and reliability is substantial. Understanding the different types of hydraulic oil seals and their specialized applications is crucial for anyone involved in the maintenance or operation of hydraulic systems. Drawing from years of industry expertise and a comprehensive understanding of the latest technological advancements, we delve into the nuanced world of hydraulic oil seals.
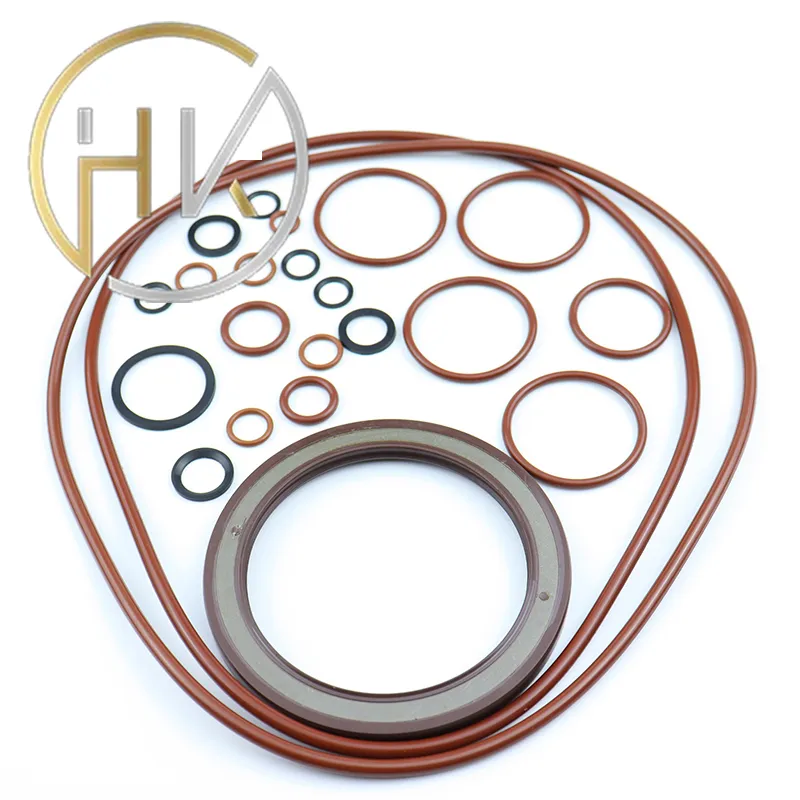
Hydraulic oil seals, by design, prevent fluid leakage and contamination ingress, maintaining pressure and ensuring system integrity. There are several types, each serving distinct purposes and suited for specific environments. The most common types include
1. Piston Seals Vital for maintaining pressure within cylinders, piston seals are engineered to prevent hydraulic fluid from leaking across the cylinder head. Common in applications requiring differential pressure, they ensure that fluid power achieves optimal conversion to linear motion.
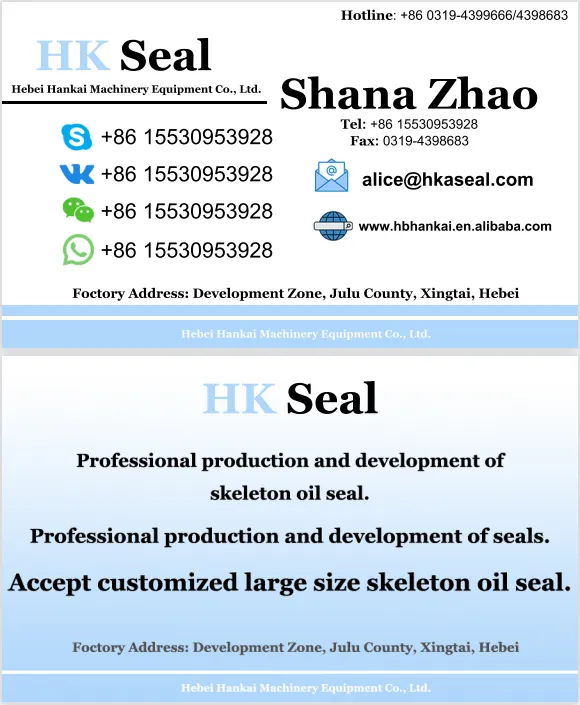
2. Rod Seals Positioned at the cylinder's opening, rod seals are key to preventing fluid escape from within the cylinder while also safeguarding the system against external contaminants. Their durability is pivotal in extending the lifespan of hydraulic systems, especially in environments where contamination control is challenging.
3. Wiper Seals Also known as scraper seals, these are installed at the cylinder head to prevent dirt, dust, and other contaminants from entering the system as the rod retracts. This is critical in dusty and dirty operational conditions, ensuring the internal components remain clean and functional.
4. Buffer Seals Designed to work in tandem with primary seals, buffer seals manage pressure spikes and fluctuations, acting as an additional barrier against high-pressure environments. Their role is crucial in safeguarding primary seals from undue strain, thereby enhancing the overall system resilience.
hydraulic oil seal types
5. Wear Rings Although technically not seals, wear rings play an instrumental role in guiding the piston and rod, preventing metal-to-metal contact that could compromise seal integrity. They provide lateral stability, ensuring seals remain effective under transverse loading conditions.
Each type of hydraulic oil seal is crafted from specific materials such as elastomers, PTFE, or polyurethane, selected based on the operational demands like temperature, pressure, and fluid compatibility. Elastomeric seals, for instance, offer excellent flexibility and resistance to thermal expansion, making them suitable for a range of temperatures and pressures. Alternatively, PTFE offers exceptional chemical resistance and low friction, ideal for high-speed applications.
The choice of hydraulic oil seal must be tailored to the specific operational conditions and requirements of the system. Misapplication or selection of inappropriate seal types can lead to premature system failure, increased maintenance costs, and unnecessary downtime. Therefore, being informed about the latest developments and innovations in seal materials and design is paramount.
Moreover, expert installation and regular maintenance are as crucial as correct seal selection. Proper installation ensures that the seals fit perfectly without undue stress, while regular maintenance checks help identify early signs of wear or damage, preventing potential failures.
Trust in a supplier or manufacturer with a proven track record of quality and innovation is also essential. Reputable manufacturers not only provide high-quality products but also offer expert guidance tailored to specific industry needs, enhancing the reliability and efficiency of hydraulic systems.
In conclusion, hydraulic oil seals, though often underappreciated, are indispensable in safeguarding the performance and durability of hydraulic systems. Understanding their types, applications, and maintenance can significantly contribute to maximizing machinery lifespan and optimizing operational efficiency. With continuous advancements in seal technology and materials, staying informed is critical to leveraging their capabilities fully.