The 80x100x10 oil seal is a vital component for maintaining machinery's efficiency and longevity. Ensuring that all parts of industrial machinery are fully protected against contaminants like dirt, dust, and moisture is crucial, especially in high-performance settings. The oil seal, despite its small size, plays a significant role in safeguarding equipment.
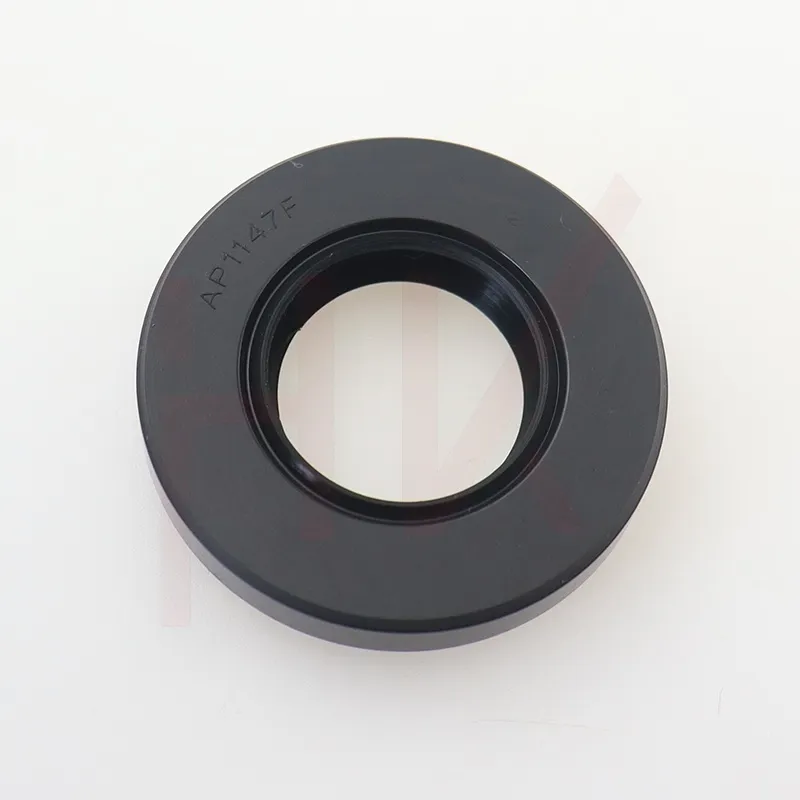
In-depth knowledge and expertise about oil seals emphasize their function in preventing the leakage of lubricants. They achieve this through their robust design, which features a flexible lip that presses against a rotating shaft.
The 80x100x10 dimension specifies an oil seal that's perfectly sized for many medium-sized machinery applications.
Selecting the correct oil seal requires understanding the specific demands of the machinery and the environment in which it operates. The 80 mm internal diameter, 100 mm outer diameter, and 10 mm width make this seal suitable for various applications, balancing high durability with ease of installation.
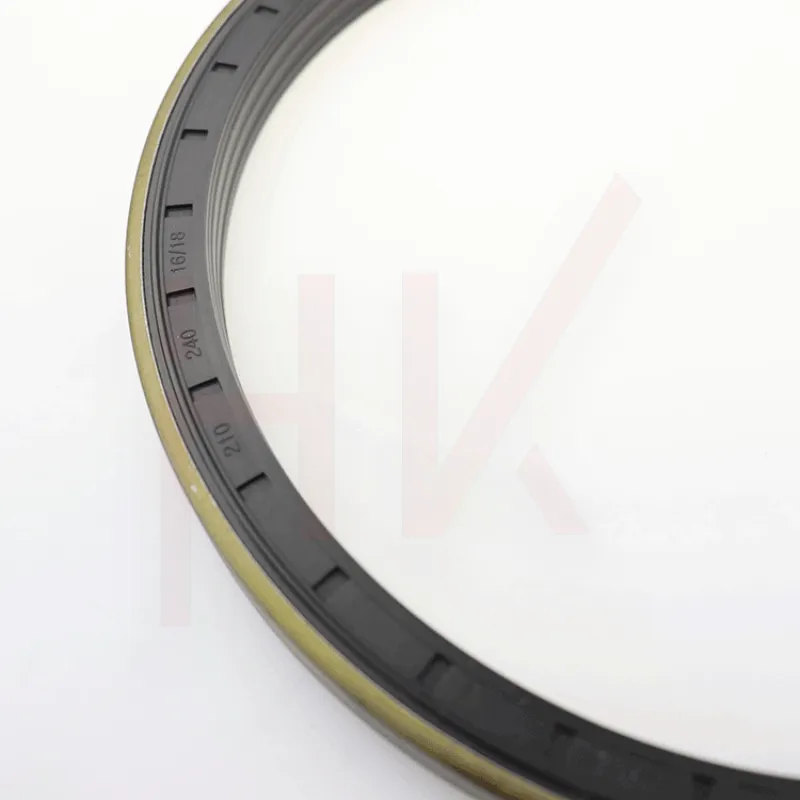
Industry specialists know that the material composition of an oil seal can affect its performance. Common materials include nitrile rubber, fluoroelastomer (Viton), and silicone, each offering different levels of resistance to heat, chemicals, and wear. For example, a nitrile rubber seal provides excellent resistance to petroleum-based oils and is suitable for temperatures ranging from -30°C to 120°C, making it an economical choice for many standard applications.
In contrast, those requiring higher temperature resistance may opt for a Viton seal, which is more expensive but performs well up to 250°C. The choice of material often depends on the machinery's operating conditions, including temperature, pressure, and type of lubricant used. Understanding these parameters ensures that the seal will not degrade prematurely, maintaining its functional integrity over time.
80x100x10 oil seal
The application of oil seals spans various industries, from automotive and manufacturing to agriculture and marine. In the automotive sector, for example, oil seals are essential in engines and transmissions, preventing fluid leaks that could lead to significant damage or inefficiencies. Similarly, in manufacturing, the presence of oil seals in heavy machinery ensures that the equipment runs smoothly and maintenance downtime is minimized.
Experts understand that incorrect installation of an oil seal can lead to premature failure, which is why proper training and adherence to installation protocols are crucial for machine operators and maintenance personnel. The use of specialized tools designed for oil-seal installation can prevent damage to the seal or the shaft, ensuring a secure fit and optimal performance.
The reliability of the 80x100x10 oil seal is also dependent on regular monitoring and maintenance. Periodic inspections can identify early signs of wear, such as cracking or hardening of the seal lip, which can compromise its ability to maintain a tight seal. In such cases, immediate replacement is recommended to avoid further damage to machinery components.
Trust in product suppliers is equally significant. Choosing a reputable manufacturer known for adhering to industry standards and providing quality products can ensure that the seals used are tested to withstand rigorous operational demands. Collaborating with suppliers who provide technical support and consultation can further enhance the reliability of machinery performance.
Ultimately, the 80x100x10 oil seal represents a small but significant investment in terms of machinery maintenance and efficiency. Employing these seals correctly can lead to cost savings over time by maximizing operational uptime and reducing the need for expensive repairs or replacements. As experts will agree, the right oil seal not only protects machinery but also enhances overall productivity.