Cassette oil seals have long stood as a critical component in numerous industrial and automotive applications, primarily due to their efficiency in preventing any leakage of lubricants. They serve to contain oil within a rotating shaft assembly, extinguishing concerns about contamination from external dust and debris, and ensuring seamless machinery function. Through personal experiences in manufacturing and frequent consultations with specialized engineers, the profound effectiveness of cassette oil seals emerges as more than just mechanical guardians.
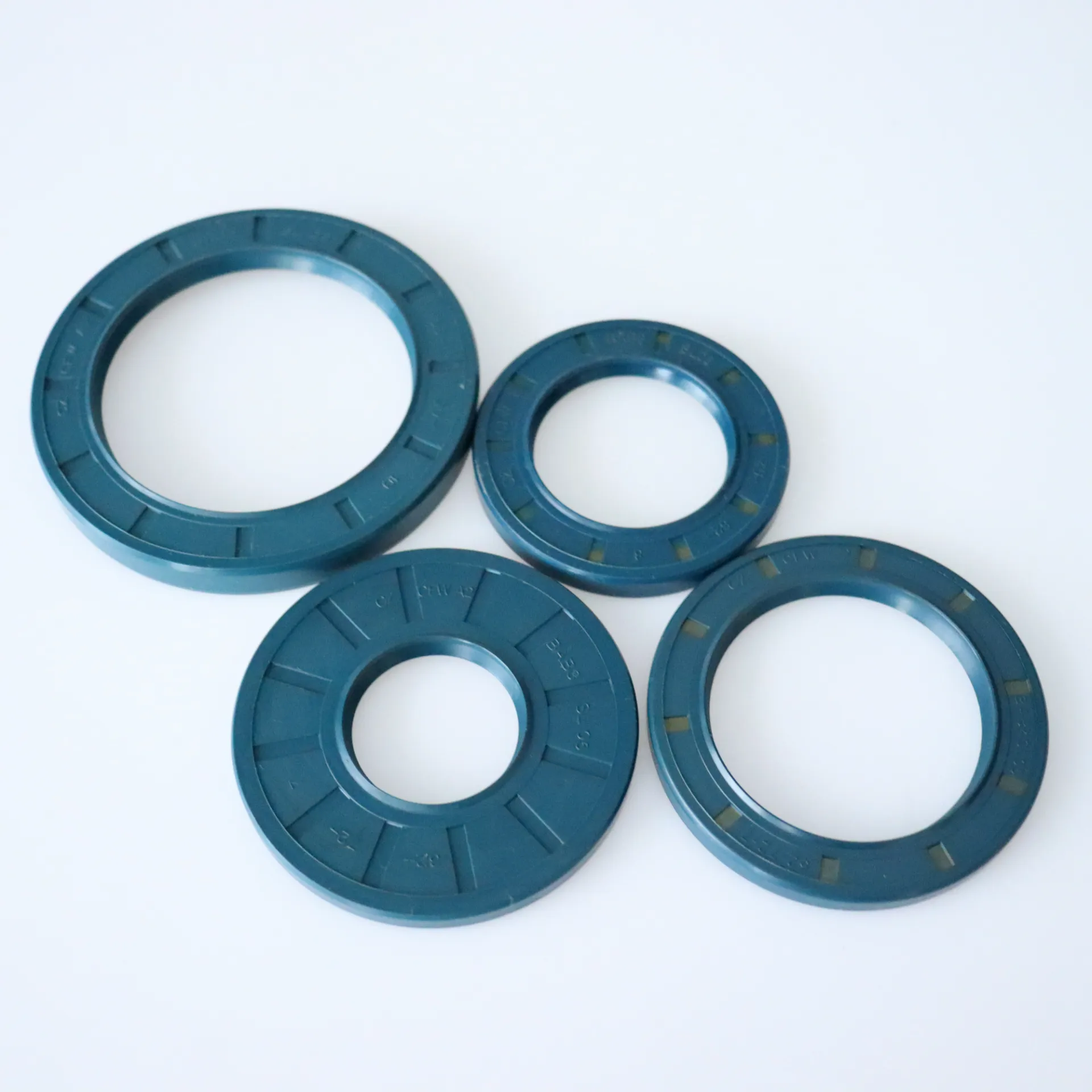
Identifying the primary advantage of cassette oil seals begins with their design excellence. Unlike traditional seals, cassette oil seals consist of an advanced multi-component system. This design includes an integral dust lip, grease cavity, and a spring-loaded sealing lip, helping to radically extend their operational life. Industrial applications demand reliability, and businesses exploiting these seals report a significant reduction in downtime, attributing this to their robust design which combats wear and tear with astonishing efficacy. This aligns with audits from seasoned professionals familiar with their installation, attesting to their durability and precision adaptability.
In the realm of expertise, the selection of high-quality materials positions these seals as an exemplar of modern engineering. Manufacturers utilize a combination of rubber composites and specialized metals, each tailored to withstand the rigors of high-pressure environments and various chemical exposures. Industries such as automotive or heavy machinery frequently experience fluctuating temperatures and pressures. Here, the resilience of cassette oil seals becomes evident, enabling operations in environments ranging from frigid cold to sweltering heat. Acknowledged experts continue to affirm that these materials not only meet but often exceed industry standards, providing a seal that endures extreme conditions without compromise.
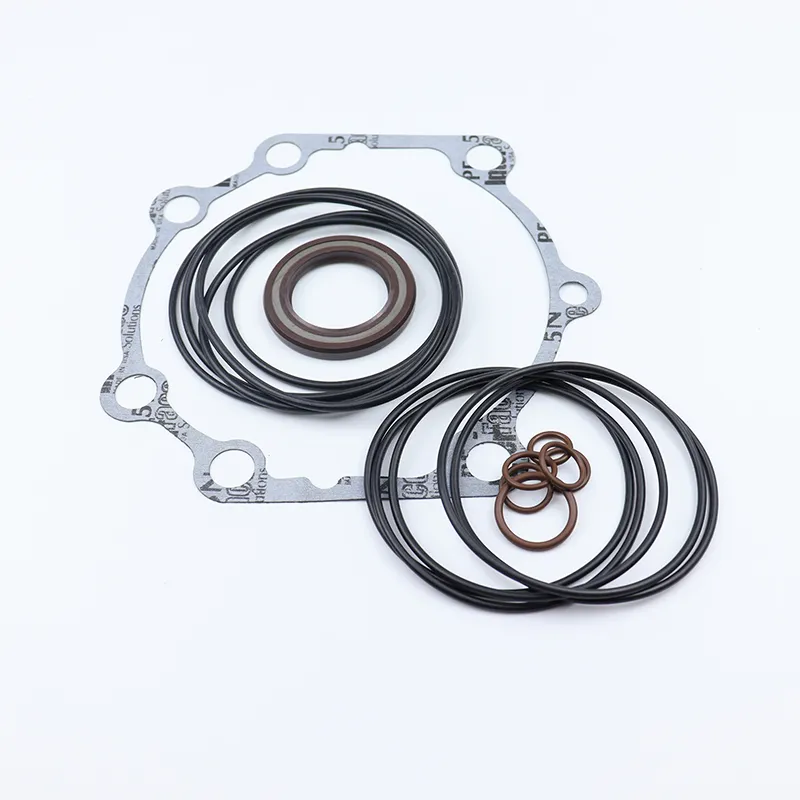
cassette oil seal
Authoritativeness in the domain of cassette oil seals can be measured by their pervasive adoption across sectors. Leading manufacturers frequently conduct research and development to enhance their utility, drawing data from diverse real-world applications. The contribution of these components to enhancing machine efficiency is supported by empirical studies and industry reports. Advising clients on machinery maintenance, engineers and technical consultants often elevate cassette oil seals as a first choice for preventing machine failure, emphasizing their validated reliability across numerous case studies and field tests.
Building trustworthiness is paramount, where ongoing collaboration with industry leaders and continuous positive testimonials stand as a testament to the credibility of cassette oil seals. Product certifications and compliance with international safety standards further solidify their trust. Manufacturers provide extensive documentation, from installation guides to maintenance tips, safeguarding users with comprehensive knowledge and instruction.
These assurances cultivate trust, attracting clientele reliant on unwavering performance.
Cassette oil seals represent a precise integration of design mastery, material excellence, and proven effectiveness. Professionals across various industries champion these components not merely for their functional benefits but for the empowerment they provide to maintain a machinery's peak performance with minimum interruptions. Whether encountering harsh contaminants or rigorous conditions, these seals indisputably stand as a tangible asset, propelling enterprise innovation and operational efficiency forward. As industries evolve, the steadfastness and enhancement of cassette oil seals continue to be a subject of keen interest and innovation, promising a future where equipment longevity and reliability are elegantly intertwined.