Navigating the world of high-temperature oil seals offers a fascinating glimpse into an essential component that guarantees efficiency and reliability in a variety of industrial applications. High-temperature oil seals are indispensable for machines that encounter extreme temperatures and demanding environments, ensuring the containment of lubricants and fluids while keeping out contaminants. This comprehensive understanding comes from years of expertise in the field, where firsthand experience has illuminated the nuanced performance of these seals.
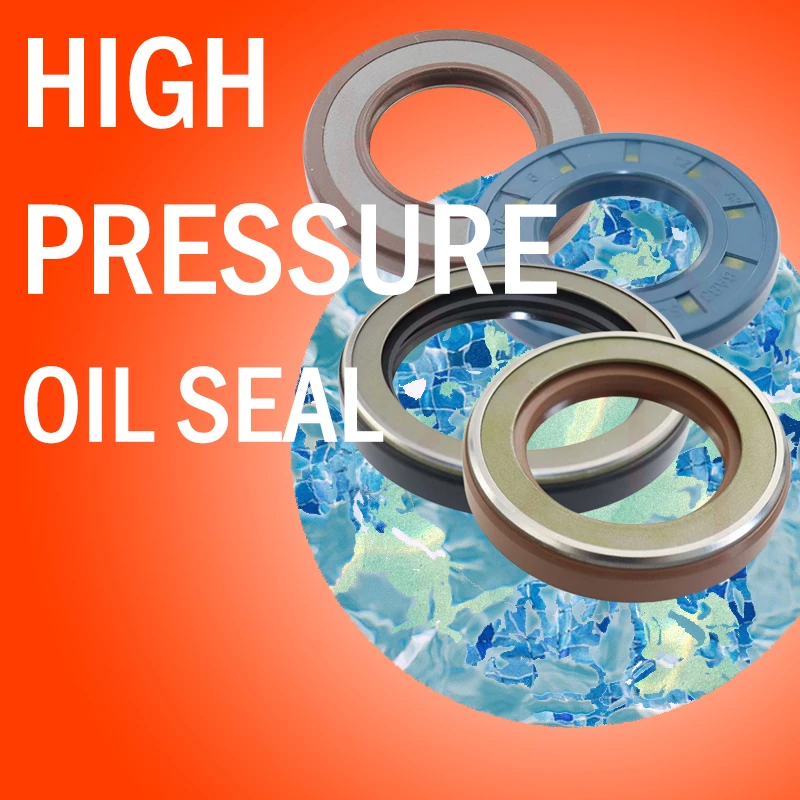
In industries where machinery is subject to elevated temperatures, traditional seals often fail, leading to leaks, contamination, or worse, complete machinery breakdowns. This inevitability underlines the necessity of high-temperature oil seals, which are designed with specialized materials such as fluoroelastomers and PTFE composites capable of withstanding intense heat while maintaining their integrity. For experts in the manufacturing and engineering sectors, high-temp oil seals are recognized not just as components but as crucial contributors to system longevity and operational efficiency.
Professionals delving into the specifics understand that the effectiveness of these seals is rooted in their design and material composition. For instance, Viton and other advanced polymers used in high-temp seals provide exceptional chemical resistance and can operate effectively in temperatures ranging from -20°F to over 400°F. This capacity allows industries such as automotive, aerospace, and heavy machinery to not only meet performance metrics but also push the boundaries of what's technologically possible.
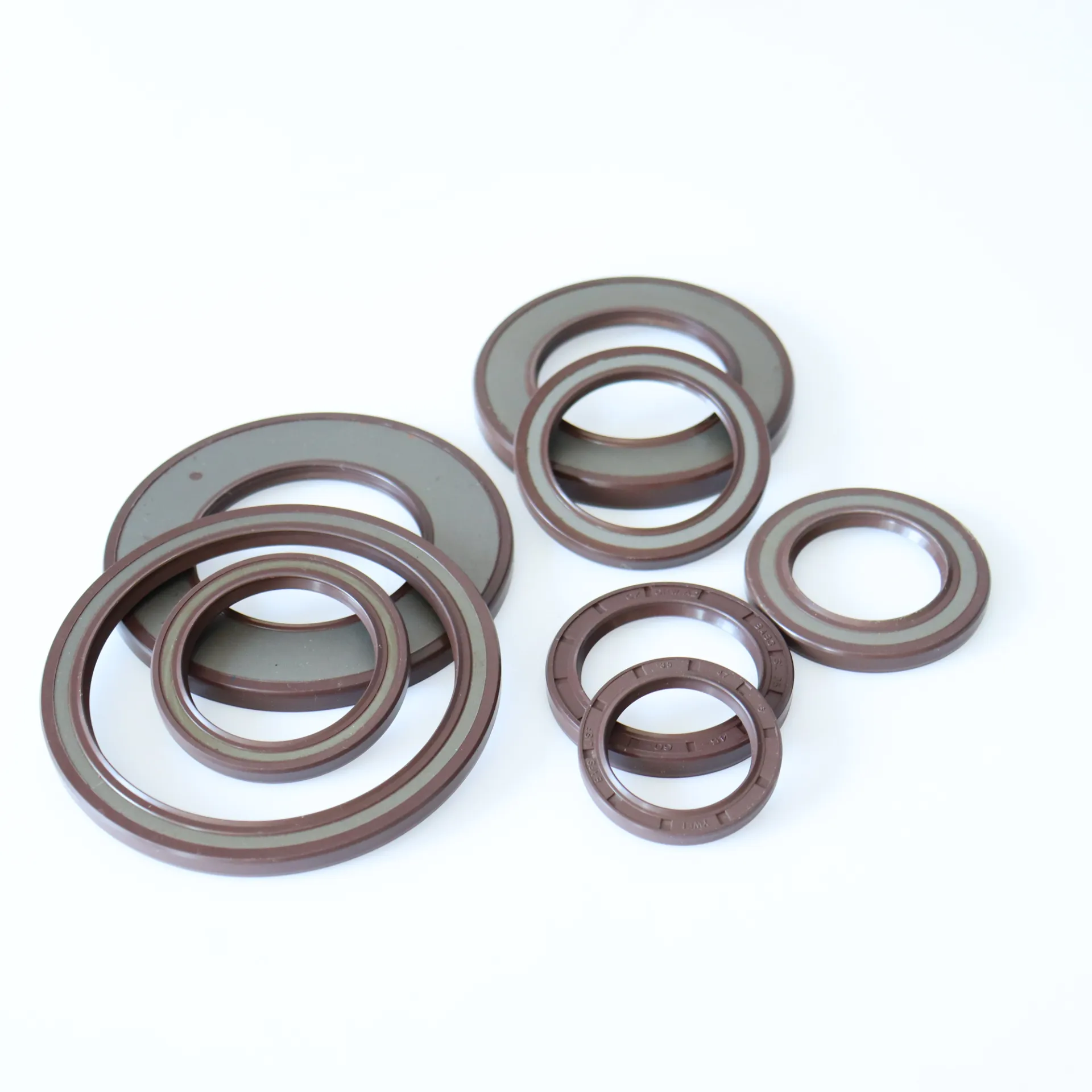
From a trusted lens of authority, choosing the right high-temperature oil seal is key to maximizing the lifespan of both the seal and the equipment. It's a decision that goes beyond just specifications; it’s about collaboration between engineers, material scientists, and industry professionals who utilize empirical data and testing to select the optimal sealing solution. Meticulous attention to the seal's environment, pressure, and chemical exposure ensures that selections made can stand the test of time and rigorous operational demands.
high temp oil seal
Incorporating high-temperature oil seals into an application is a process backed by both science and engineering accuracy. Once installed, ongoing monitoring and maintenance are vital to uphold their performance. Experienced professionals advocate for regular inspections, checking for signs of wear or degradation. Such vigilance is fundamental, supporting the TRUST element, as businesses depend on seamless operation without unexpected interruptions.
Establishing a reputation of reliability and expertise in the oil seal industry comes from successful integration experiences and validated performance outcomes. Companies that have made high-temperature oil seals a cornerstone of their product offerings deliver not just a product, but a promise of durability. Through rigorous research, practical applications, and continuous innovation, they provide solutions that align with industry needs, thereby fostering trustworthiness among their clientele.
Ultimately, the specialized world of high-temperature oil seals represents the intersection of engineering prowess and industrial necessity. By leveraging both scientific advancements and practical know-how, industry leaders continue to build upon a foundation of experience, expertise, and authority, creating pathways for innovation that maintain trust and push boundaries in equal measure.