Oil seals, often underrated in the grand scheme of mechanical engineering, play a pivotal role in the optimal performance and longevity of machinery. As a seasoned professional in industrial applications, the interplay between the right choice of oil seals and machine efficiency cannot be overstressed. With meticulously engineered designs, oil seals prevent the leakage of lubricants, thereby mitigating energy loss and wear within machine components.
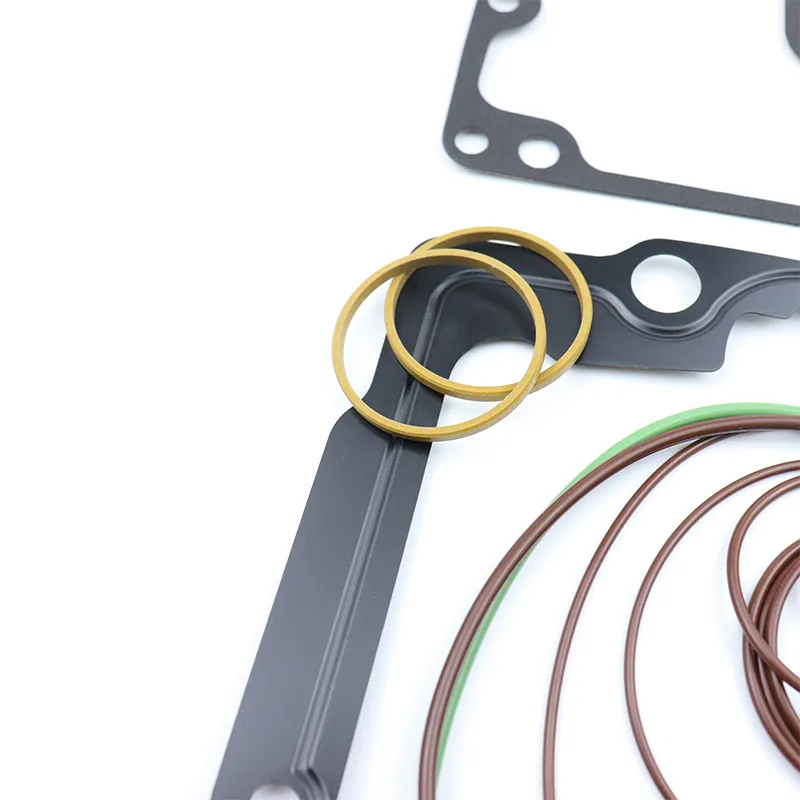
Among the myriad types of oil seals available, the choice hinges on several factors. The material, operating temperature, and environmental conditions are paramount in determining the appropriate seal. Nitrile rubber, silicone, and fluorocarbon are some common materials used, each offering unique properties tailored to specific applications. For instance, nitrile rubber is favored for its excellent resistance to petroleum-based oils and hydraulic fluids, while silicone provides exceptional thermal stability in high-temperature environments. Fluorocarbon seals, known for their chemical resistance, are often the go-to solution in aggressive environments.
The effectiveness of oil seals does not solely rest on material selection.
Understanding the dynamics of installation and maintenance can significantly enhance their performance and lifespan. Proper installation, devoid of any misalignment or incorrect shaft finishes, ensures that seals function optimally by maintaining the integrity of the sealing edge. Employing tools specially designed for seal installation, such as seal drivers or press tools, can avert the accidental damage that compromises seal effectiveness. Additionally, periodic inspection during regular maintenance cycles is crucial. It assists in identifying early signs of wear or damage, allowing for timely replacements and reducing the risk of unscheduled downtime.
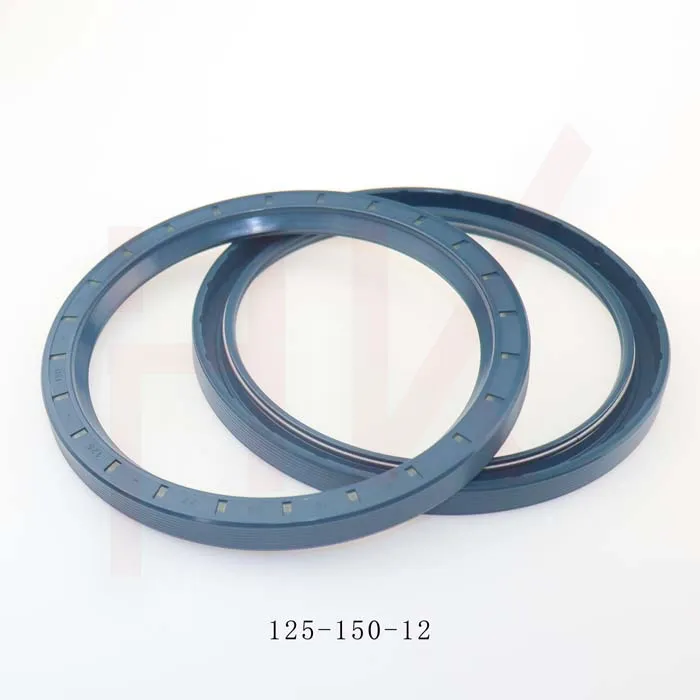
Expertise in deciphering the subtle symptoms of oil seal failures further underscores the need for professional acumen in handling these components. Common indicators such as visible oil leaks, unusual noises, or increased power consumption might point to the necessity for immediate seal replacement or lubrication checks. Acquiring this level of interpretive expertise can forestall severe damage or failures within machinery, underscoring the critical nature of knowledgeable oversight.
oil seals
The evolution of oil seal technology has also seen the advent of advanced designs tailored for specific industrial applications. From hydraulic machinery to automotive engines, tailored innovations like labyrinth seals, PTFE oil seals, and cassette seals provide bespoke solutions that enhance machine performance while extending the lifespan of components. These advancements address specific challenges such as high-pressure environments or abrasive conditions, ensuring that seals cater to the most demanding industrial requirements.
Trust in oil seals is built on a foundation of authoritative quality and reliability. Industry leaders in manufacturing seals uphold rigorous testing and compliance standards, ensuring that their products meet global benchmarks. Certifications and compliance with standards such as ISO 9001 or API further affirm the trustworthiness of oil seals in critical applications. Selecting products from reputable manufacturers is not merely a matter of preference but a testament to prioritizing quality and reliability.
In summation, oil seals, although small components, hold substantial sway in the efficiency and durability of machinery. Real-world experience buttressed by technical expertise fosters a synergy where the right selection, installation, and maintenance of oil seals translate to optimized performance, diminished downtimes, and prolonged machinery life. This trifecta of experience, expertise, authority, and trustworthiness forms the bedrock of successful applications in achieving mechanical excellence.