Forklift hydraulic cylinder seals are pivotal components in the operation of industrial lifting vehicles. These small yet crucial parts ensure the hydraulic system's efficiency, reliability, and longevity, reflecting the intricate synergy between precision engineering and robust performance. Understanding their function, maintenance, and replacement can significantly enhance operational safety and extend equipment lifespan.
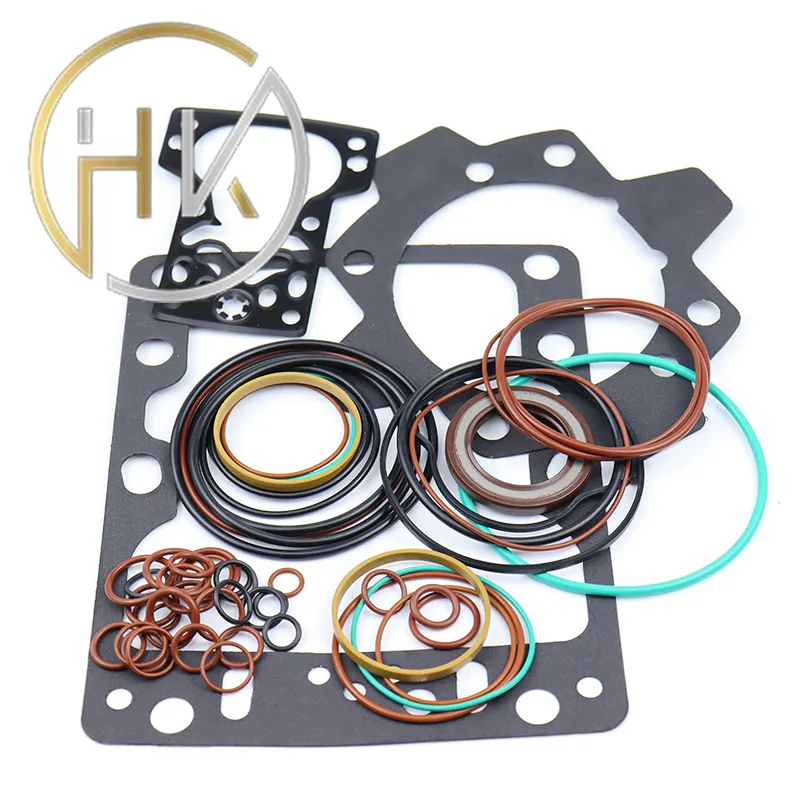
Hydraulic cylinders are vital in converting fluid power into mechanical power within forklifts, enabling smooth and precise lifting actions. The seals within these cylinders are responsible for maintaining the necessary pressure, preventing leaks, and keeping contaminants at bay. Their failure can lead to inefficient operations, costly downtimes, and safety hazards.
To underscore their importance, let's delve into the manufacturing materials and design specifications of these seals. Typically crafted from polyurethane, nitrile rubber, or fluoroelastomer, the material choice depends on the operational environment and specific forklift applications. Polyurethane seals, for instance, offer excellent abrasion resistance, making them ideal for heavy-duty applications. Nitrile rubber seals are preferred for their oil resistance, suitable for more general conditions. On the other hand, fluoroelastomer is favored in high-temperature environments due to its exceptional heat and chemical resistance.
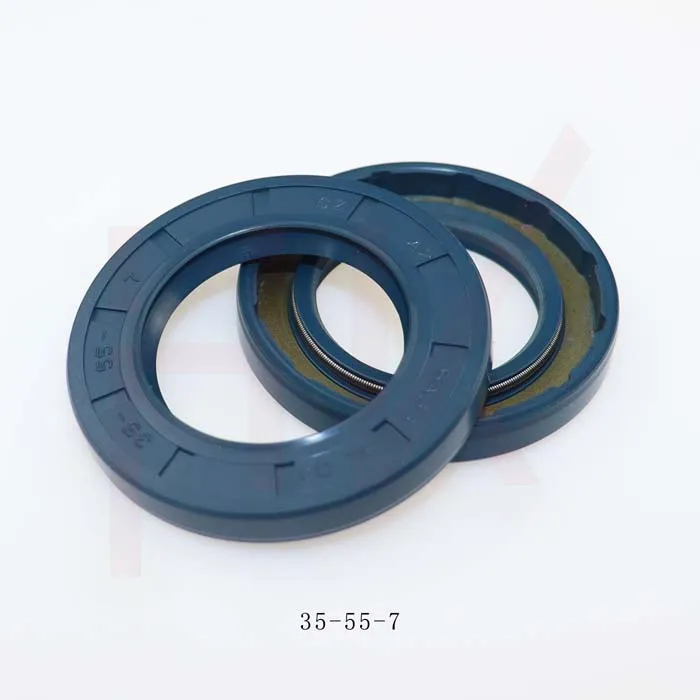
Selecting the appropriate seal involves considering factors such as temperature fluctuations, pressure requirements, and exposure to chemicals or contaminants. Using the wrong type of seal can lead to premature wear and system malfunction, underlining the importance of expertise in seal specification.
From a maintenance perspective, regular inspection of hydraulic seals is critical. Signs of wear, such as cracks, tears, or deformations, suggest a need for immediate replacement. Scheduled maintenance should incorporate a thorough examination of seals to mitigate unexpected breakdowns that can disrupt warehouse operations. Utilizing expert technicians for assessment can ensure a more accurate diagnosis and prevent unnecessary replacement costs.
forklift hydraulic cylinder seals
When it comes to replacement, precision and adherence to manufacturer specifications are non-negotiable. Deviating from these can compromise the hydraulic system's integrity, leading to diminished forklift performance. Using original equipment manufacturer (OEM) parts guarantees compatibility and reliability. Additionally, educating forklift operators about the signs of hydraulic seal failure can preemptively address issues before they escalate.
To establish a reputable supply network for replacement seals, partnering with trusted suppliers who offer genuine products is key. Counterfeit or substandard seals not only jeopardize system efficacy but can also pose significant safety risks. Brands that have garnered a reputation over years for quality assurance and superior customer service should be prioritized.
Harnessing expertise in hydraulic systems ensures operational efficiency. Those in the logistics and supply chain sectors should prioritize continuous learning about the latest developments in seal technology and maintenance techniques. This proactive approach fosters a competitive edge, empowering businesses with the reliability and foresight necessary in an environment where operational consistency is paramount.
Trust in hydraulic cylinder seals for forklifts is built over time, with consistent performance and stringent quality checks. By investing in premium seals, businesses commit to operational excellence and uphold safety standards, enhancing their reputation as industry leaders. With expert guidance and a data-driven approach to seal management, companies can confidently steer their fleets toward optimum productivity and safety compliance.
In conclusion, forklift hydraulic cylinder seals, though often overshadowed by larger components, play an indispensable role in ensuring seamless operations in material handling environments. Their proper selection, maintenance, and replacement is a testament to a company's commitment to maintaining high standards of safety and efficiency. By focusing on these critical aspects, businesses can achieve not only operational excellence but also forge a path of innovation and authority in the industry.