Hydraulic motors play a pivotal role in various industrial and mobile applications, converting hydraulic energy into mechanical energy to power machinery efficiently. One of the critical components ensuring the optimal performance and longevity of these motors is the hydraulic motor seals. These seals are not merely supplementary components but are essential for the precise and sustained operation of hydraulic systems.
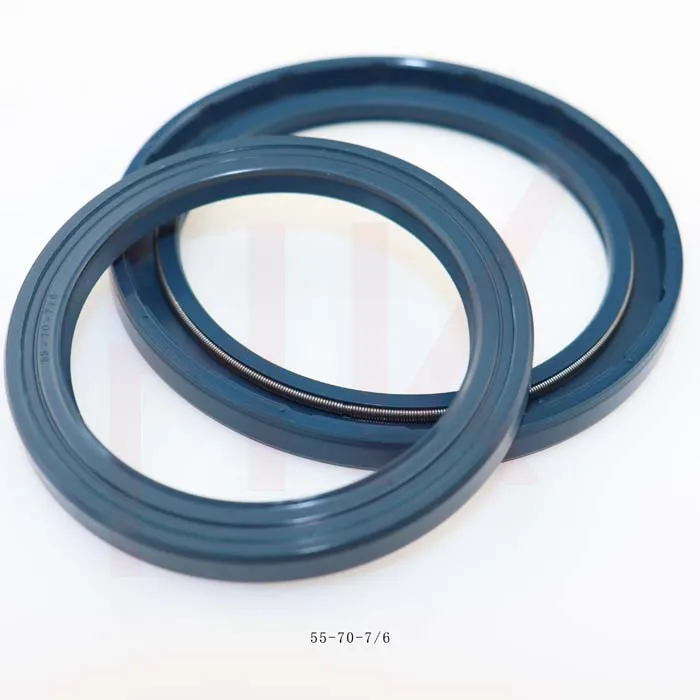
The significance of hydraulic motor seals primarily lies in their ability to withstand extreme conditions. Hydraulic systems often operate under high pressure and varying temperatures, both of which can compromise a seal's integrity over time. High-quality seals are engineered to resist these pressures while maintaining their flexibility and resilience. Expertise in selecting the right seal material, such as nitrile rubber, Viton, or polyurethane, is crucial for specific applications. The choice of material directly impacts the seal's performance, resistance to chemical degradation, and ability to prevent fluid leakage.
Field experiences have demonstrated the paramount importance of understanding the operational environment when choosing hydraulic motor seals. A leading hydraulic system engineer shared a case involving a construction application where incorrect seals led to frequent system downtimes. The seals used were not optimally designed for the abrasive nature and temperature fluctuations found in such demanding environments. After careful analysis and the selection of more robust, temperature-resistant seals, the reliability of the system increased significantly, reducing maintenance costs and enhancing equipment uptime.
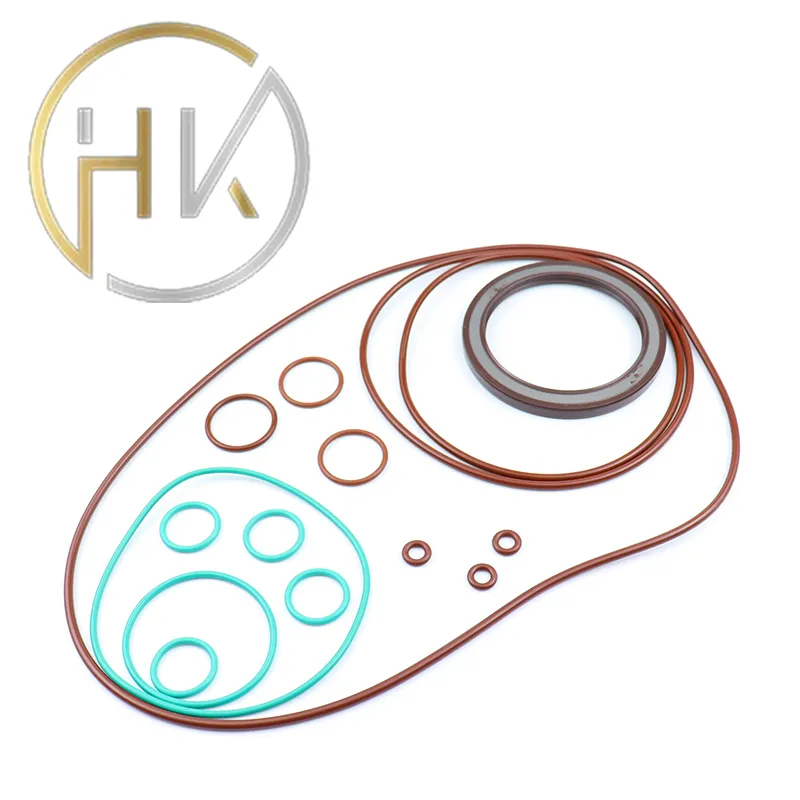
Professional expertise in hydraulic systems underscores the necessity of regularly monitoring seal conditions. Routine inspections can prevent unexpected failures and extend the motor's lifecycle. The early detection of wear and tear allows for timely replacements, which not only safeguards the equipment but also optimizes operational efficiency. This proactive approach reflects best practices embraced by industry leaders, who prioritize sustainability and reliability in their operational strategies.
hydraulic motor seals
Manufacturers also play a critical role in ensuring the authoritativeness and trustworthiness of hydraulic motor seals. Collaborations with reputable manufacturers provide assurance of quality and innovation. These manufacturers invest in research and development to create seals that meet international standards and certifications, suggesting reliability and superior performance. The integration of advanced technological solutions, such as self-lubricating seals and seals with embedded sensors for real-time monitoring, represents cutting-edge advancements that cater to the evolving needs of industrial applications.
Trust in hydraulic motor seals is enhanced by leveraging case studies and testimonials from recognized industry leaders. These real-world applications affirm the reliability of premium seal products, providing new clients with confidence in their investment. By highlighting successful implementations and measurable outcomes, companies can build a reputation for quality and dependability in the competitive market of hydraulic components.
In conclusion, the selection and maintenance of hydraulic motor seals are of paramount importance for the proficient and sustained operation of hydraulic systems. With a blend of field experience, professional expertise, reliable manufacturing, and innovative technology, businesses can ensure the efficiency and dependability of their hydraulic equipment. Emphasizing these critical factors not only enhances operational productivity but also reinforces the reputability and competitiveness of enterprises within the industry.