Oil seals, often referred to as rotary shaft seals or radial lip seals, are essential components in various machinery. These seals specifically designed for the 35 47 7 dimensions provide critical functions in the longevity and efficient operation of equipment, making them a topic of significant interest for engineers and maintenance professionals alike.
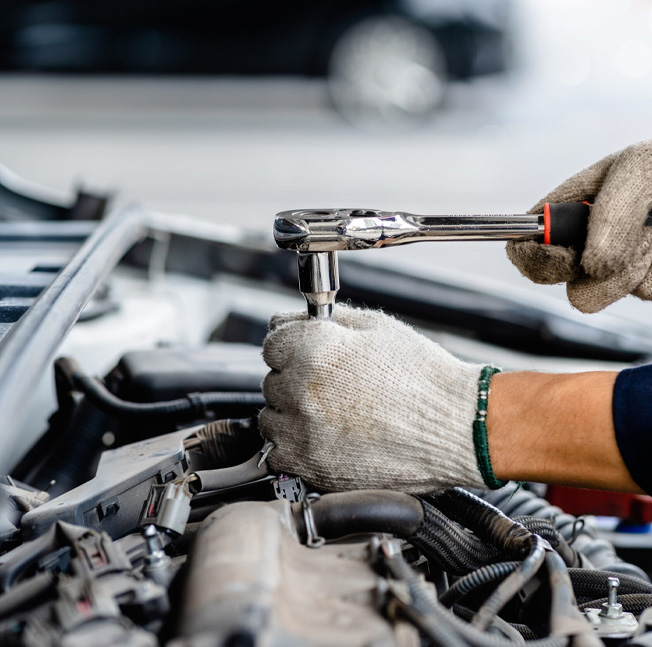
Oil seals serve best when preventing the leakage of lubricants and the intrusion of contaminants such as dust, dirt, or moisture. The 35 47 7 oil seal denotes a seal with an inside diameter of 35mm, an outside diameter of 47mm, and a width of 7mm. This precise specification ensures compatibility with a wide array of machinery, from industrial applications to automotive engines.
In industries where machinery undergoes constant operation, the choice of an appropriate oil seal like the 35 47 7 can have a profound impact on machine performance. For instance, in automotive applications, oil seals play a critical role in preventing oil leaks in engines and gearboxes, which might otherwise lead to reduced efficiency and eventual mechanical failure. Experience shows that choosing the correct size and material can prevent common maintenance issues. Additionally, the installation process should be handled precisely to avoid misalignment, which could compromise the seal's integrity and function.
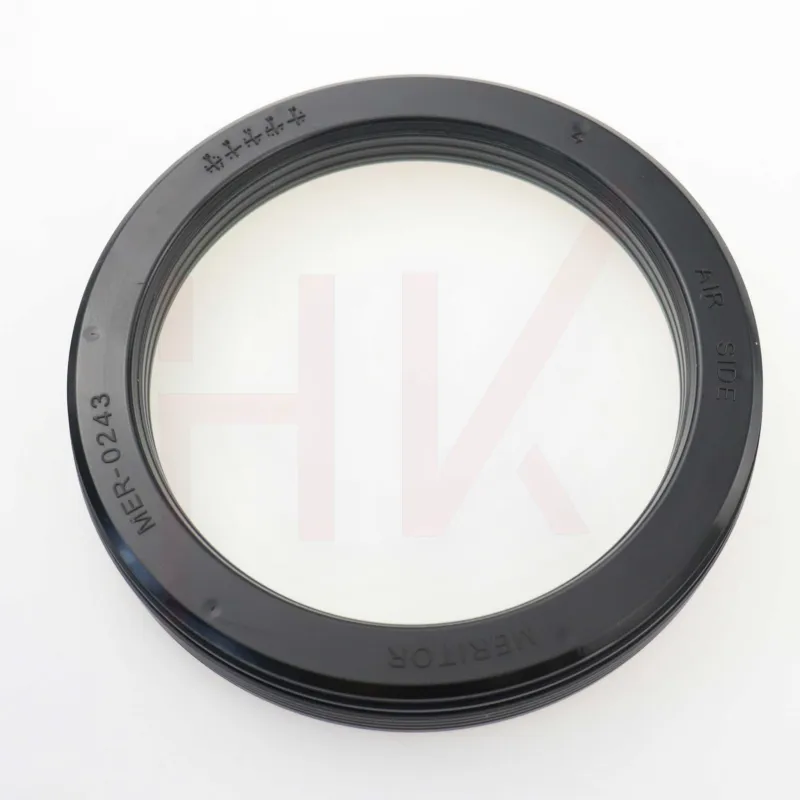
Professional expertise is vital when selecting and maintaining oil seals. Engineers must consider the environmental conditions to which the seal will be exposed. Factors such as temperature extremes, chemical exposure, and pressure variations dictate the material choice for maximum durability. Nitrile rubber, for example, is highly resilient to oils and fats at moderate temperatures, but for more extreme conditions or chemically aggressive environments, a move towards viton or silicone seals might be more appropriate.
Authoritativeness comes into play with the manufacturers of these oil seals. Reputable manufacturers often provide data sheets detailing material properties, testing results, and recommended applications. Industry certifications and adherence to international standards also bolster the manufacturer's credibility, ensuring users that their 35 47 7 oil seal has undergone rigorous testing for durability and performance.
35 47 7 oil seal
Trustworthiness is built through consistent performance over time. End users report that high-quality oil seals significantly reduce downtime and maintenance costs. However, regular inspections remain essential to catch wear or damage early. Visual checks for cracks or hardened materials can prevent excessive wear on rotating shafts. Trustworthy suppliers often offer technical support and guidance, ensuring that users can maximize the lifespan and efficacy of their oil seals.
Moreover, advancements in seal technology continue to enhance their effectiveness. Recent innovations include the development of low-friction materials and enhanced seal lips designed to reduce energy consumption and heat generation. These improvements are particularly important in high-speed applications where traditional seal materials might fail.
Ultimately, the success of utilizing the correct 35 47 7 oil seal depends on a holistic approach—assessing environmental factors, understanding technical specifications, and engaging with reputable suppliers. Professionals drawn from extensive backgrounds in mechanical engineering, maintenance, and procurement regularly contribute to valuable insights and advancements in this field, driving innovations that meet the ever-evolving demands of modern machinery.
In a world where efficiency and reliability are paramount, the strategic selection and proper maintenance of components like oil seals are crucial. To ensure machinery runs smoothly and efficiently, investing in high-quality oil seals and staying abreast with technological developments proves indispensable for industries across the spectrum.