Hydraulic pump seals play a crucial role in ensuring the efficiency and longevity of hydraulic systems. These seals are designed to prevent fluid leakage, maintain pressure, and protect against contamination, which are all vital for optimal system performance. Understanding the importance and functionality of hydraulic pump seals can lead to better maintenance, reduced downtime, and ultimately, cost savings.
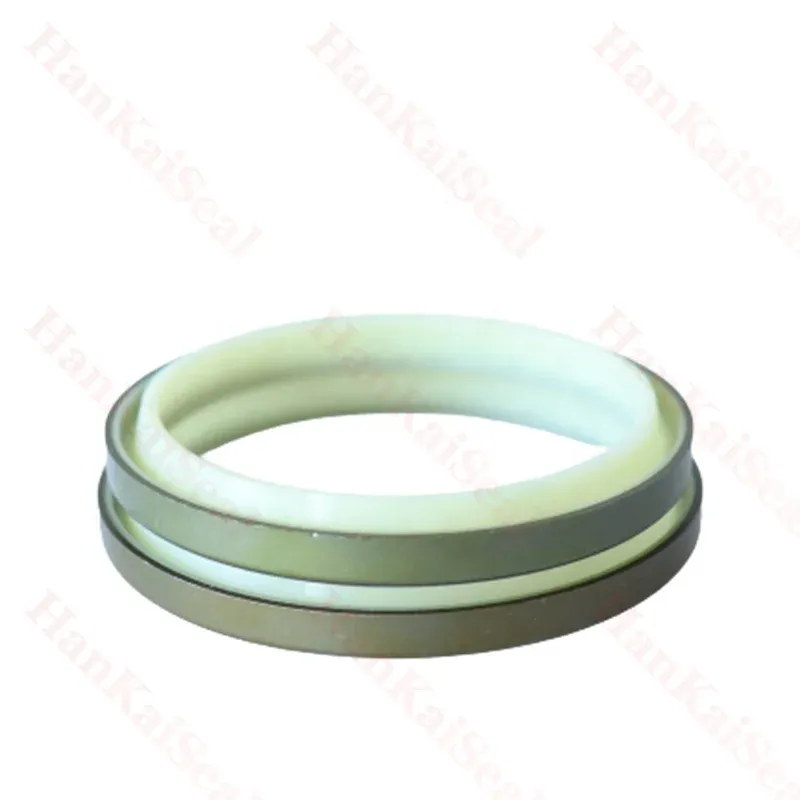
Firstly, hydraulic pump seals are engineered to withstand high pressure and temperature variations that occur in hydraulic systems. These seals are commonly made from materials such as nitrile rubber, polyurethane, and PTFE, each offering distinct advantages depending on the application. For instance, nitrile rubber is often used for its robust resistance to petroleum-based oils, while polyurethane provides exceptional abrasion resistance, making it ideal for applications with significant mechanical wear.
The expertise required in selecting the right seal involves a thorough understanding of the system's operating conditions. This includes parameters such as fluid type, temperature ranges, and pressure levels. An experienced engineer or technician will assess these factors to recommend seals that will not only ensure functionality but also extend the operational lifespan of the hydraulic system.
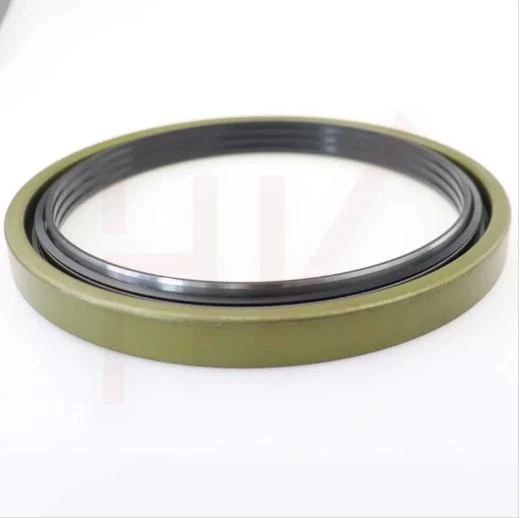
Proper installation of hydraulic pump seals is another critical aspect that can affect their performance. Misalignment or improper installation can lead to seal failure, causing leaks and potential contamination. Therefore, it's imperative to follow manufacturer guidelines or consult with professionals who have substantial knowledge in hydraulic systems. Utilizing correct installation tools and techniques can help avoid premature seal wear and system inefficiencies.
hydraulic pump seals
Regular maintenance and inspection of hydraulic pump seals are essential to ensuring system reliability. Seals should be inspected for any signs of wear, cracking, or other forms of damage. Scheduled maintenance checks allow operators to identify potential issues before they lead to more serious failures. It is also advisable to maintain records of seal replacement and maintenance activities, which can aid in identifying patterns of wear and facilitating proactive maintenance strategies.
Authoritative providers in the hydraulic seal industry often impart valuable insights through technical articles, guides, and support services, empowering users with knowledge on best practices and innovative technologies. Collaborating with reputable suppliers who offer quality seals and responsive support can instill confidence in users, knowing they have reliable resources to maintain their systems efficiently.
In terms of trustworthiness, using OEM (Original Equipment Manufacturer) seals can be pivotal. OEM parts are designed specifically for the equipment they are fitted to, ensuring compatibility and optimum performance. Moreover, when warranty is a concern, OEM seals can often be verified for authenticity and quality assurance, thereby safeguarding the investment in hydraulic machinery.
In conclusion, hydraulic pump seals are not mere components but integral parts that ensure the smooth operation of hydraulic systems. A comprehensive understanding of their function, careful selection based on system requirements, proper installation, and regular maintenance are essential practices that enhance system efficiency and reliability. By leveraging the expertise of seasoned professionals and adhering to authoritative guidelines, businesses can ensure long-term savings and operational success through effective management of hydraulic pump seals.