Hydraulic gear pump seals are a critical component in the efficient functioning of hydraulic systems, serving the essential purpose of preventing fluid leakage. Understanding the importance of these seals, their types, and proper maintenance techniques can profoundly impact the overall performance and longevity of hydraulic equipment.
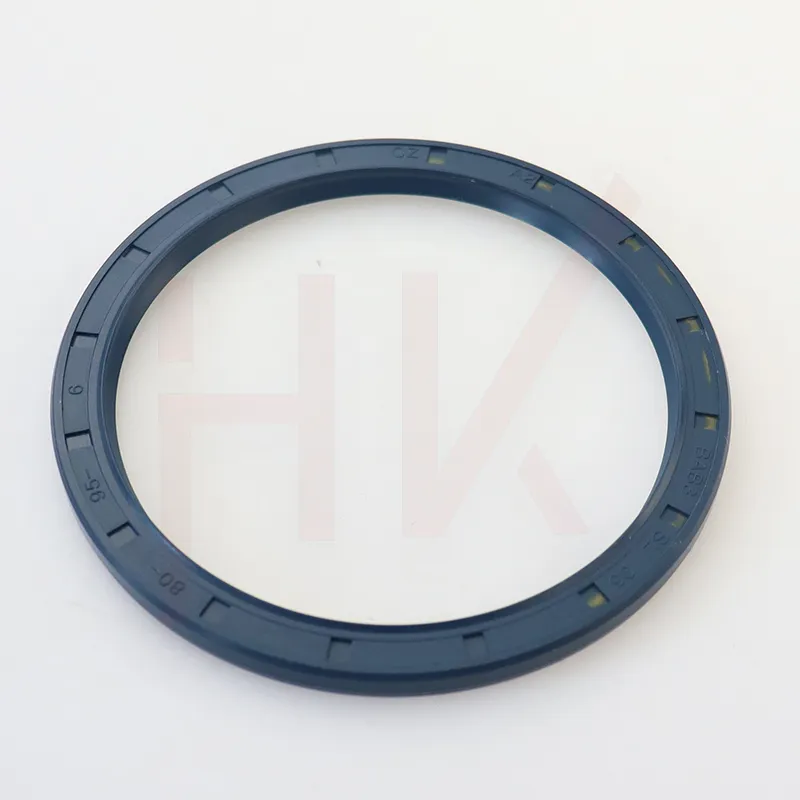
In the world of hydraulics, maintaining the integrity of a hydraulic system is paramount. One cannot overlook the seals, which play a crucial role in ensuring the system operates efficiently without any leaks. These seals are specifically designed to withstand high pressure and temperature conditions that are typical in hydraulic applications, making them indispensable for engineers and technicians who depend on these systems.
Hydraulic gear pump seals come in various types, each suited for different applications. Commonly used seals include O-rings, gaskets, and lip seals. O-rings are circular sealing elements typically used in static applications to prevent leakage between two or more parts. They are versatile and cost-effective, making them popular in various industries. Gaskets, on the other hand, are used to create a seals between two or more stationary components. Their primary function is to prevent fluid or gas leaks, which can be detrimental in hydraulic systems. Lip seals are dynamic seals that are designed to retain fluids within a housing containing a rotating, reciprocating, or oscillating shaft, making them essential in mobile equipment where movement is constant.
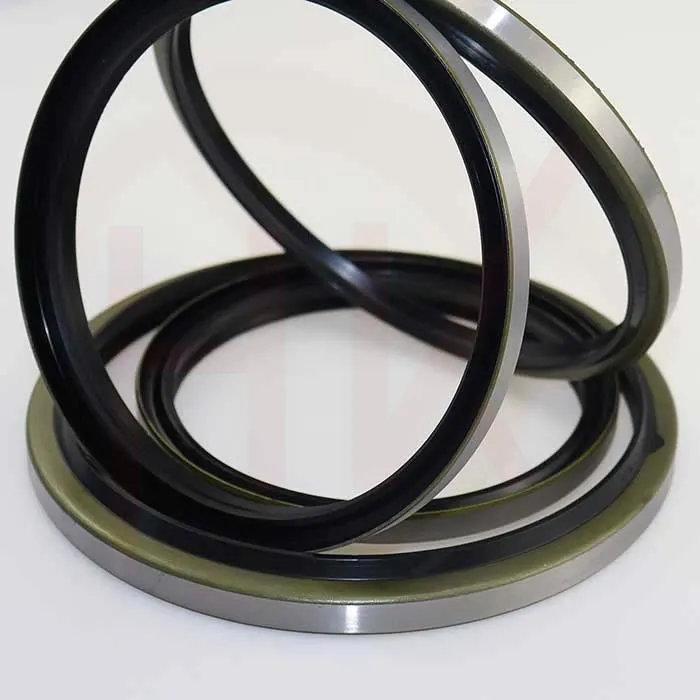
The selection of hydraulic gear pump seals often depends on the specific requirements of the application. Factors to consider include the type of fluid used, pressure levels, temperature ranges, and the materials' compatibility. High-quality seals made from durable materials such as polyurethane, PTFE, or elastomers should be considered to withstand the rigorous demands of hydraulic applications.
Routine maintenance and inspection of hydraulic gear pump seals are vital to ensure optimal system functionality. Regularly checking the seals for signs of wear, tear, or damage can help prevent unexpected failures, which can lead to costly downtime. It's crucial to replace seals at the first sign of leakage or wear, even if it seems minor. Ignoring such indications can result in severe hydraulic fluid loss and potential damage to the entire system.
hydraulic gear pump seals
Moreover, proper installation of seals is fundamental. During installation, ensure that the seals are correctly aligned and fit snugly into their designated grooves. Utilize the recommended tools to avoid damaging the seal material, which might compromise their effectiveness. Misalignment or improper installation can lead to premature seal failure and, consequently, system inefficiency.
Another factor influencing the performance of hydraulic gear pump seals is the cleanliness of the hydraulic system. Maintaining a contamination-free environment within the system significantly enhances seal performance. This includes regular filtration of hydraulic fluid and ensuring any foreign debris is promptly removed. Contaminants can rapidly degrade seal materials, lose their integrity, and result in leakage.
For industries heavily reliant on hydraulic systems, investing in high-quality seals ensures reliability and efficiency. Cutting corners with cheaper, inferior seals may appear cost-effective initially but can lead to more significant expenses in terms of maintenance and potential system failures.
Consulting with professionals and relying on experts in seal manufacturing can provide tailored solutions specific to individual hydraulic system needs. Many companies offer consultative services that suggest the right type of seal based on detailed system analyses.
Overall, hydraulic gear pump seals are not just minor components but pivotal elements that significantly determine the longevity and efficiency of hydraulic systems. By prioritizing the selection, installation, and maintenance of these seals, businesses can assure the operational continuity of their hydraulic machinery, reducing unexpected disruptions and ensuring a smooth workflow.